Die-casting is one of the most versatile and efficient manufacturing processes used in industries such as automotive, aerospace, electronics, and consumer goods. It allows manufacturers to produce complex, high-precision metal parts with excellent surface finishes and dimensional accuracy. However, despite its widespread use, many people still find the process somewhat mysterious. In this blog post, we’ll break down the key aspects of die-casting, explain how it works, and outline what you need to know if you’re considering this method for your project.
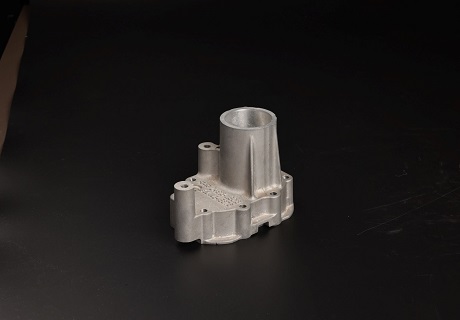
What is Die-Casting?
Die-casting is a metal casting process in which molten metal is injected under high pressure into a steel mold (also known as a die) to form a part. The process is typically used for metals with low melting points such as aluminum, zinc, and magnesium. Die-casting produces parts that are precise, strong, and lightweight, making it an ideal solution for manufacturing components that require intricate detail and high-volume production.
The Die-Casting Process
The die-casting process involves several key steps, each contributing to the final quality of the product:
- Preparation of the Die: The die, typically made from steel, is designed and built to the specifications of the part to be produced. It is carefully cleaned and lubricated to prevent the molten metal from sticking and to ensure smooth removal of the finished part.
- Molten Metal Injection: Once the die is prepared, molten metal is poured into the injection system. A plunger forces the metal into the die cavity at very high pressure (up to 4500 psi), ensuring that the metal fills all the details of the mold.
- Cooling and Solidification: After the molten metal fills the cavity, it is allowed to cool and solidify. The cooling time depends on the complexity and size of the part. Once solidified, the die is opened, and the part is ejected.
- Finishing: After ejection, the die-cast parts may undergo additional finishing processes such as trimming, polishing, or machining to remove excess material and ensure the part meets the required specifications.
Types of Die-Casting
There are two main types of die-casting processes: hot-chamber die-casting and cold-chamber die-casting.
- Hot-Chamber Die-Casting: This method is typically used for metals with low melting points, such as zinc. The melting pot is integrated with the injection system, allowing the molten metal to be directly injected into the die. This process is faster and more efficient but is limited to metals that don’t corrode the injection system.
- Cold-Chamber Die-Casting: In this method, the molten metal is poured into a separate chamber before being injected into the die. It’s commonly used for materials like aluminum and magnesium, which require higher melting temperatures. Cold-chamber die-casting is more versatile but slower than hot-chamber die-casting.
Advantages of Die-Casting
Die-casting offers a wide range of benefits, making it a popular choice for manufacturers across various industries:
- High Precision: Die-casting is ideal for creating complex parts with tight tolerances and intricate designs.
- Excellent Surface Finish: The smooth surface finish achieved during the casting process often requires little or no additional post-processing.
- High Strength-to-Weight Ratio: Die-cast parts are lightweight yet strong, which is particularly beneficial for industries like automotive and aerospace.
- High Production Speed: Die-casting is well-suited for high-volume production, allowing manufacturers to produce large quantities of parts quickly and cost-effectively.
- Cost-Effective for Mass Production: The initial setup cost for die-casting molds can be high, but the cost per unit decreases significantly in large production runs, making it a cost-effective option for mass production.
When to Use Die-Casting
Die-casting is ideal for parts that require high strength, precision, and a smooth finish. Common applications include:
- Automotive Components: Engine parts, transmission cases, and body parts.
- Aerospace Parts: Structural components, brackets, and housings.
- Consumer Electronics: Housing for phones, laptops, and other devices.
- Industrial Applications: Machinery components, valves, and housings.
However, it’s important to note that die-casting may not be the best choice for every project. It is most suitable for projects with high-volume production needs, where precision and detail are essential.
Challenges in Die-Casting
While die-casting is an efficient process, it does come with its challenges:
- Initial Tooling Costs: The cost of designing and manufacturing the molds can be high, which may not make die-casting cost-effective for low-volume production.
- Material Limitations: Die-casting is typically limited to metals with low melting points, so it’s not suitable for all types of materials.
- Porosity: If not properly controlled, die-casting can result in tiny air pockets within the metal, which can affect the strength and durability of the part.
- Complexity of Design: While die-casting is great for producing complex parts, there are still design constraints that need to be considered, such as wall thickness and draft angles.
Die-casting is a powerful manufacturing process that offers a wide range of benefits, including precision, strength, and cost efficiency for high-volume production. Understanding the key steps and considerations involved can help you decide whether die-casting is the right choice for your project. If you’re considering die-casting for your next manufacturing need, it’s essential to work with experienced professionals who can guide you through the process, from mold design to finished part production.
For more information on die-casting and how it can benefit your manufacturing process, feel free to reach out to our team. We specialize in custom die-casting solutions and can help bring your vision to life with precision and efficiency.